Mill refurbishment, underground bins, power generation plant at Nutrien Rocanville: Contractor workforce to peak at 1,000 this year
June 8, 2021, 2:18 pm
Kevin Weedmark
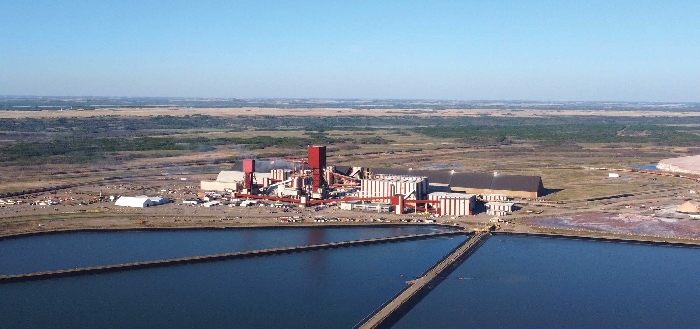

Work is under way on refurbishment of the original mill at Nutrien Rocanville. The start of the project was delayed by Covid-19 last year. Work is also under way on replacement of some underground components including the raw ore bins, and on development of a power generating plant on the site.
The projects will bring a lot of contractors to the site, with the number peaking at between 500 and 1,000 for each of the next three years.
“We celebrated our 50th anniversary back in September and we still have areas of our operating plants that are from day one,” said Nutrien Rocanville General Manager Shannon Rhynold.
“We did the major expansion and we brought a new mill on line in 2016 but the old mill—mill one as we call it—still has areas of operation and portions of it that are still original.
“So when you look at the projects over the next few years, the big one that we’re doing on site is a refurbishment of our original mill. Each time we take out some of the old technology and put in something new there’s a potential for investment. We question how do we improve on this. With a lot of the projects that we are doing, it’s a bit of a chess match. We’re trying to make sure we can keep the operation running while replacing equipment. We use our turn around strategy (when operations cease for a few weeks for major maintenance) to do tie-ins. A lot of the work that’s going on out here right now is some of that replacement work. It’s things like raw ore bins and ore galleries and new electrical and the re-feed of all those cables from new buildings into old infrastructure. We have two production hoist systems as well and one of them was upgraded during the expansion, the old original one still has the original electrical drive components. So we’re doing an upgrade this year to upgrade our hoists to modern drive technology. So that will be another one that we tie in during our turn around this year.”
Multi-year project
So how big of a project is this?
“It’s going to be in the hundreds of millions of dollars, and we’re going to spend that over numerous years,” says Rhynold. “Easily over the next five years we’re going to spend a couple hundred million dollars investing into just the refurbishment of our mill. On top of that if there are investment opportunities that make sense, if you come up against a bottleneck opportunity where a new piece of equipment can solve an issue, there could be some additional costs.
“There’s a lot of work on the surface, and when I look at the underground, we run into some similar issues. We’ve got our original shaft area. It’s still there. We’re doing a lot of work now on replacing the original bins underground and this is a massive undertaking that requires a lot of mining, a lot of rehab mining, but also we’ve created three new ore storage bins underground. Those are currently being cut with a plan to tie those in and connect everything again by the turn around 2022 window.”
Self-generation project
Nutrien is also investing in a power generation plant at the Rocanville site. TransGas installed a gas pipeline to its facility near Moosomin to the Rocanville mine site last summer.
“We put in the gas line last year. We didn’t delay that one with Covid-19 but we did push off the Self Gen project itself, and now we’re back into site prep and we have the foundations laid for the generators when they do arrive,” says Rhynold. “Those generators are actually on their way to Canada. I believe they’re on the ocean right now as we speak. They will be arriving on site this summer, sometime towards the end of June, and they’ll be placed on the concrete pads and we’ll be completing the work to actually build the building around it once they arrive. We’ll get them on the pads, we’ll build the building and we’ll start the electrical tie in during our turn around this year as well, when we can shut down the power.
“The commissioning of the generation project will be next year. The project schedule has it ending mid 2022, although we’re confident we can bring it on ahead of that. The gas line is done, it’s sitting there, it’s ready to be tied into. We’ll do the electrical tie ins during our turnaround this year and then it’s just a matter of getting the training and commissioning under way. We’re budgeting and planning to turn it on in 2022.”
Crews building up as work progresses
“We always see a build up of contractors particularly as we get close to our turn around,” says Rhynold. “Throughout a big part of the year we’re carrying probably 200 contractors per day on average throughout the year and as we ramp up closer to our turn around, which will happen mid-September and October this year, we’ll peak likely around 1,000. One of the challenges that we always see and we try to work with the project team is just on ‘where do you put everybody?’
“We reach out and we work with the RM and we make them aware of the numbers and we reach out to all the hotels and campgrounds and provide a list of all of the places to stay within a 100 km radius. It gets tight, so we hit that peak and it may only be for a week or two during the turnaround when you’re trying to get all the major tie ins done, but those are big numbers and we see it on our parking lots and we see it in our communities. It’s something that we are cognizant of and do try to make sure that people are aware that there is this flood of contract employees coming.”
Some crews have been in the area since early spring.
“I think you’re seeing it build up now,” said Rhynold. “The self gen group, the teams working on that, they really started to mobilize at the end of March into April and we’ve seen a bit of a bump in their numbers, just in the last month or so, as construction ramps up and prep ramps up for the delivery of those generators. Other projects will be similar. You’ll start to see in July and August, that ramp up occur, but we really don’t peak until you get into the turn around itself and that’s when it’s full out, everyone’s on site, the plant is down for that four to five week window, and day and night you’re trying to maximize as much work as you can.
“It gets tight. The capacity’s there for 1,200 to 1500 people within 100 km. That’s filling hotels, in Saskatchewan and Manitoba all the way up to Virden. Within the Nutrien network we try to offset our turnaround so that labor is available but we also try to make sure we’re somewhat offset with what Mosaic does, so we’re not having all the contractors coming at the same time, so the contractors can go between sites and plan to be here a little longer if there’s work at both operations.”
Projects for next three years
2021 to 2023 will all be busy construction years.
“I would say 2021 to 2023, we’re going to see similar levels with peaks of 500 to 1,000 contractors on site,” said Rhynold. “We’re hitting on some of those big projects like raw ore bins, ore galleries as part of this re-furb to our old mill. The re-furb plan stretches into 2023 and we try to level the spending over that time. I would guess for the next couple years we’re going to see this level of activity on our site, and in 2024 or 2025 we start to see the decline. The major components of the re-furb will be done, so the numbers do start to drop a little bit at that point.
Plan in works for two years
“We’ve been planning the re-furb for a couple of years,” says Rhynold. “We actually were ready to execute on it last year and so that raw ore bin, the ore gallery were projects that we deferred from last year into this year.
“With any project within a company like Nutrien there’s a certain amount of capital for all the sites. We really break down the project, we follow the certain buckets and you’re always going to be allocated a certain amount of sustaining capital which is really meant to protect the integrity of your assets. That’s a given.
“There is the other aspect though, when you look at things like self gen, that’s an investment. That is investment dollars that you compete for within the network and within the organization as a whole. And within those, you look at what value are we going to generate. When we look at self gen for us, there are many reasons to do it. The first reason really is, it’s the right thing to do and I think our ability to take natural gas and generate electricity from that, it really is going to reduce our emissions, our carbon footprint is going to go down. You’re eliminating that requirement for coal fired power, buying from the grid. It becomes more efficient for us, it’s better for the environment and it is cheaper, it will save us money and build efficiencies to burn natural gas to generate that electricity versus buying it off the grid. It also fits very nicely within Nutrien’s overall plan—we want to help reduce emissions. So with this project we reduce our carbon footprint by not buying that coal-fired power, and also build efficiency and cost savings.”
Rocanville Nutrien’s cornerstone
“Rocanville’s a critical part of Nutrien’s potash network,” says Rhynold. “We have a great network, we’ve got six very flexible low cost mines, but since the expansion finished here in late 2016, Rocanville really has become the cornerstone for the network. I’ve heard people call it the flagship. We continue to produce, since that expansion, 40 to 45 per cent of the network’s annual production and we do it as the low cost producer. We are the flagship, we’re the anchor. We drive safety, we drive innovation, and continuous improvement for the company.
“Across Nutrien, we are the low-cost producer, but credit to my peers at the other sites, they’re pushing us. They’re all bringing their costs down as Nutrien becomes more efficient and decides to be strategic in how we run our operations. We’re really getting pushed. Some of the operations have had the odd month where they’ve beat us. Overall we’re still holding that position but it’s important to keep focusing on continuous improvement. Nutrien talks a lot about next generation potash and the things that fall into that. And those are things like automation and self-generation and advanced process control in our mills, and those are the things we try to take a lead on, but the network itself is pushing that direction. So we are the low cost producer right now and we’re going to do our best to hold onto that position.”