A tour of Nutrien Rocanville, the world’s largest potash mine
November 26, 2024, 11:20 am
Ashley Bochek
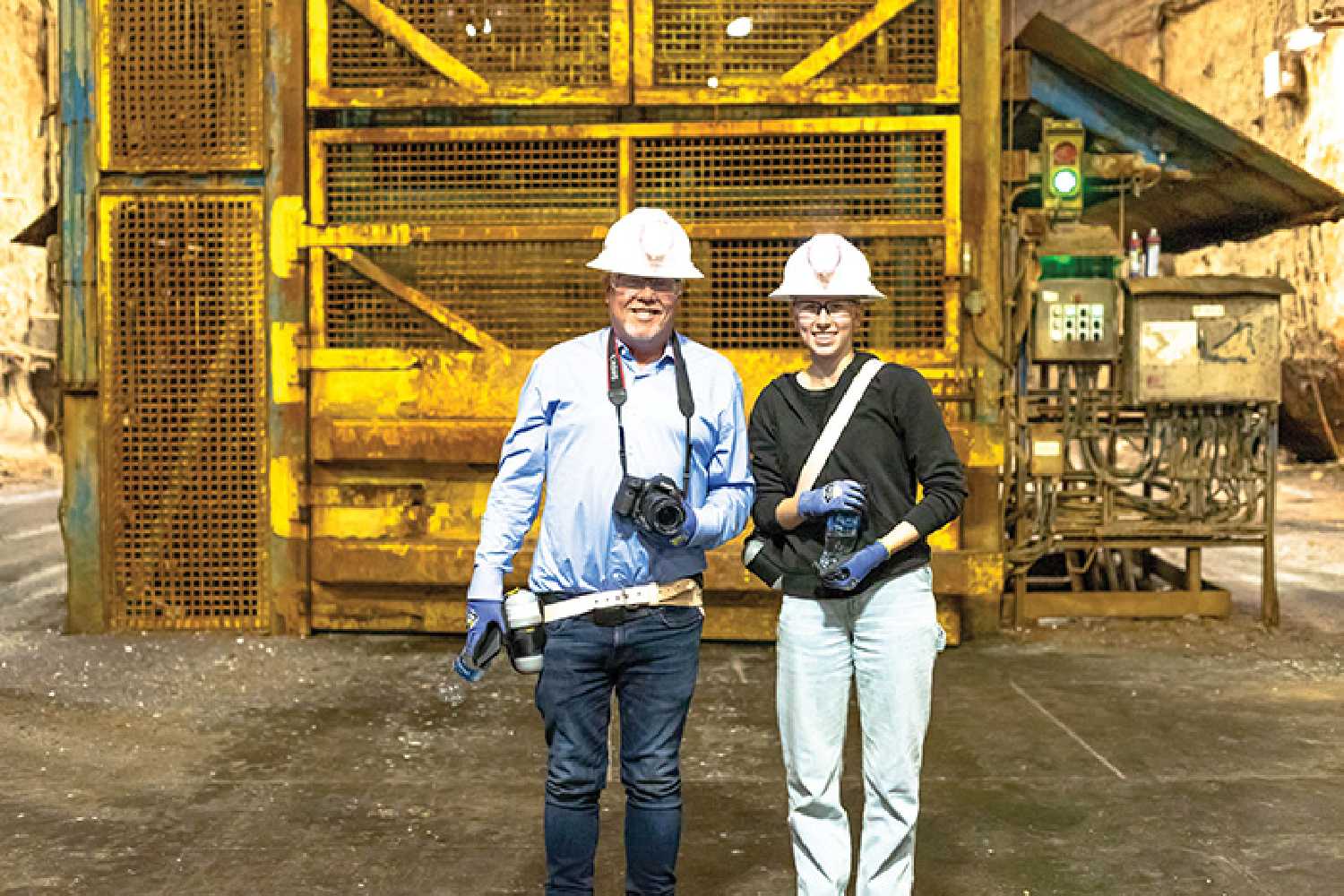

The Nutrien Rocanville mine held the first family tour since before Covid in August of 2024. Family members of miners and two representatives of the World-Spectator toured underground and learned about how the mine operates.
Justin Young, General Manager of Rocanville Mine, explains his position at the mine.
“I am the General Manager at Rocanville. I have been with the company since 2011. I have worked in various capacities over the years. I started as a mining engineer, then took over the completion of the Rocanville West expansion. I went and worked in the mill in the maintenance department. Then, I became the assistant GM where I oversee the mine and the mill, and then most recently, for about the last year I have been GM. As general manager duties, I am responsible for the operation in its entirety for Rocanville—mining, hoisting, milling, and loadout—a little bit of everything. You have to know a little bit about each department, not a lot about one thing. You have to surround yourself with good people that manage the day-to-day operations. The way I see my job, is I am the filter between the corporate office and the site. They have certain initiatives and agendas and I filter that to make sense for our site in Rocanville and then I am also filtering out information from the site to corporate.
“Typically I am in Saskatoon likely once every three weeks, but I am stationed in Rocanville either on the Scissors Creek side or I am at the mill side. I have an office in each and I try to split my time 50/50 between the two.”
Mining potash
Young explains Rocanville’s approach to mining.
“We start with our ore body and before we even start mining, we do a 3D-seismic of the area to make sure we know what we’re expecting for geology because you never want to get into a situation like we did in the ‘80s where we didn’t know what we were up against and we ran into anomalous ground, which was water bearing and risked flooding our mine. Thankfully they were able to stop it.
“After 3D-seismic, the mine engineer takes a look at the body of reserves and what is the most efficient and effective way to mine it. Then, we create our mine plans—it is handed over to mining operations and they execute. They will set up their panels, we call them, and they’re mining off a panel belt onto an extensible belt back to the shaft. Our mining method is long room and pillar—that means we cut three passes. You cut the first pass with the mining machine and you’re building the belt behind the miner. Then we anchor what we call a tail-pully—you turn the miner and go back the direction you came from, that is the second pass. Then, we jump the belt and cut the third pass to the end of the room and then just turn the miner back. How big the rooms are depends on the geology and the area you’re in. On average, about 5,000-6,000 feet.”
Young explains they use conveyor belts to send the potash from the mining machines to the mill, several kilometres away.
“From there, it goes onto the belts. We have a network of conveyor belts that is approximately 75 kms of mainline conveyors throughout the mine to get it back to the mill. The mill is 17 kms as the crow flies back to the east and there we have two hoists, where we hoist it to the surface. It is stored in bins underground—similar to a grain bin on surface except this is cut in rock—we dump it in those bins and then hoist it to surface through those two skips. Then, it goes through the milling process, where it is crushed, sized, cleaned, dried, and then it goes into a storage bin on surface or it could get loaded out right away, typically it goes right into those large storage bins and then we load from there into trains.”
Background of mine
Young says the Rocanville mine employs many people from surrounding communities. “Underground and surface combined we have about 860 people from the area and others from all over.”
He says the mine was built 54 years ago. “The Nutrien mine in Rocanville was built in September of 1970, that is when the first rail car was loaded. We started operations at Scissors Creek in November of 2016. We announced the expansion and the new shaft in 2007 for Scissors Creek, and we completed it in 2016. We sunk the Scissors Creek shaft, and we also built mill two at the same time back at the original site. It was all part of that expansion, but then we also had to add to our underground network. We had to get more mining machines to double our throughput. It was 26 conveyors underground throughout to set up panels and then build shops and all the electrical infrastructure,” Young said.
Huge local operation
Young explains the Nutrien Rocanville mine ships large amounts of potash by train every day.
“We are shipping close to on average 20,000 tonnes a day. We could load a little more than that. Typically on a good day if the demand is there, we will load out what we produce because if we didn’t, we would fill our barns. We average 16,500 tonnes a day and then loading close to 20,000 if the demand is there. We are slated to produce about 5 million tonnes this year and our nameplate capacity is about 6.5 million tonnes.”
Young says the mine ships many tonnes of potash to the west coast to be shipped to other countries.
“For us at Rocanville, 70-80 per cent of our product is domestic. Some goes to Canada, but mostly to the United States. It is shipped via rail to the states. The remainder of it goes through what we call, Canpotex, and that goes for the most part out to the west coast port in Vancouver. It is sold to China, India, whoever Canpotex has contracts with.”
Challenges underground
Young says there are challenges that come when working underground.
“In mining, you are mining into the unknown a lot of the time—there is seismic, but you really don’t know what you have until you’re mining into it. You know that you’re not hitting anomalous ground, but sometimes you don’t know how the ground is going to react to mining so there are always those concerns, the geological formations you’re mining into. Thankfully, we have a strong mining engineering team that manages that with the support of operations. There are so many moving parts, there is 75 kms of moving conveyor and if one of your conveyors goes down toward the shaft you aren’t mining anywhere else because you can’t get the raw material off, so there is always maintenance that you’re up against. We have superintendents that manage that for us now. Then, you have a workforce of 800 some people so there’s always the people you’re managing. It takes all kinds of people to run a potash mine.”
Young says that transportation is one of the biggest challenges for the mine.
“If you were to ask me yesterday what the biggest challenge is, I would have said the rail strike because that has a huge impact on our business. The majority of our material is shipped by rail, and it seems like every year we have one of those type of disruptions. It is either on the rail or on the port so that is always something we are watching. We do understand there are a few other contracts coming up.
“We are seeing strong demand for potash right now, but with that the price is somewhat soft so that is a bit of a challenge. Based on forecast, we are expecting strong demand again next year because potash is pretty affordable right now. Looking at some of our competitors, at some point we are going to see the war on people, where you’re fighting over skilled and qualified tradespeople and professionals. We haven’t quite seen that yet, but I anticipate in coming years that will be more of a challenge.”
New mines means competition for employees
Young says with the new mines coming to Saskatchewan Rocanville mine hasn’t seen an impact on recruitment yet, but that might change.
“For our operation we haven’t really seen much of a draw from our resources to BHP. It is probably more of a concern for Lanigan because they’re neighbours up there. We haven’t seen them hire many full-time people. They are still a couple years away from production so it is obviously a concern of ours, but right now we haven’t seen too many people leave. I am sure once we get closer to the fourth quarter of 2026 or the first quarter to 2027 when it comes online. Prior to that you’ll probably see more of a pull, but I think our northern mines up by Saskatoon will be most impacted. Certain positions are harder to come by. It is trying to attract young engineers, young professionals that is tougher especially if they go to school in a bigger centre like Toronto or Saskatoon where you have friends and you don’t want to leave that. We have been fortunate, we have a few folks that are somewhat from around the area then we get them on board and sometimes they may have a significant other who is also a professional and we get them on board so we were pretty lucky here last year. Then, there is some competition for talent in terms of mechanics and electricians.”
Tours encourage a learning experience for all
Young says the mine is a lot bigger than what people think.
“I don’t think people understand how big of a footprint we actually are underground, and understand what goes on to make it all work, but that is why we do tours, to get our younger generation from the area that we anticipate the kids that we tour may work at the mine at some point, but it also gives an opportunity for kids like my own son to see what dad does and where dad works. Thankfully, we are allowed to do this, because we haven’t been able to do these tours for awhile.”
He said because of the location of the mine not everyone is aware of the operation and how significant it is.
“It is an awareness thing—it is hidden underground. It is hidden north of Rocanville, unless you were to drive by it you would never really know it is there.”
Young says the mine’s footprint is as big as the city of Saskatoon. “We use lots of tactics to explain the rough size of the mine, but a good comparison is if you overlaid our mine over the city of Saskatoon map you would see it is about the same size and as we continue to expand to the west, the overlay of our mine would almost overlay the city of Calgary so if you put it into reference of how big Calgary is or how big Saskatoon is that is the footprint of our mine.
He says Nutrien Rocanville mine has more than a dozen mining machines.
“We have 15 miners in our fleet. Typically for us to hit our production plan we’re running about nine in a day depending on the mining sequence some are turning, some are down for preventative maintenance.”
Largest potash mine in the world
Young says the mine at Rocanville is the biggest potash mine in the world.
“The Nutrien mine at Rocanville, in terms of volume, ranks number one in Saskatchewan, and is the world’s largest potash mine.
“Mosaic did claim that they were the largest, but it didn’t pan out with their Canpotex numbers. They have the biggest footprint of a mine, but we produce more.”
He explains, “The Nutrien assets alone produced around 13-14 million tonnes last year and global demand is around 68-72 million tonnes. We have seen growth about 2.5-2.7 per cent year-over-year. There are years that is down, but always seems to be followed by a year or two where it is up.”
Not what people expect
Young explains the mine is different from what most people may think.
“Everybody pictures a mine where you go into this little tunnel, it is really dark, you can touch the walls on either side, there are rocks falling everywhere, it’s wet and it’s cold, and then you come to Rocanville and it is actually quite the opposite. Our rooms are 8-9 feet tall, 26 feet wide would be our narrowest room, some are up to 66 feet wide, you get off the cage (the shaft) and it is almost 30 feet high by 40 feet wide. It’s a lot more open and a lot more air moving than people would expect. I think that would be the biggest wow factor. People never picture this underground. They’re expecting they’re going to go into this small little hole and they get out in a open area.”
Future expansion
Young says the mine sees increasing global demand for potash going forward.
“We’re seeing the global growth in demand equal to what the tonnes are coming online from other competitors or other people in the business. By the time we see BHP coming online the global demand for potash—based on 2-3 per cent growth—will be able to absorb those tonnes. So for us, I see our site running roughly about the same going forward. You would have to spend a lot of capital expenses to upgrade things and it probably makes more sense to invest in some of our other facilities at this point. I see steady as it goes right now and we will be continuing to move to the West.”
He says the Rocanville mine will see future expansion at some point.
“There are lots of considerations for a shaft, it is a very large capital investment for that type of infrastructure—when you’re spending that kind of money you’re doing a lot of feasibility studies to make sure you’re spending the right money, at the right time, on the right things. There are other solutions to power, we have things called power wells that is an encased hole and you stick your power feed down. Then, you’re seeing the push for electric vehicle fleets. If you’re moving to electric vehicle fleets you’re depleting the amount of diesel particulate matter in the air so you need less ventilation ultimately. There are certain things that can bridge us to the point where you would need to do a new shaft so I think we are a long way from announcing anything like that, but in a mine our size, you’re always looking at all of the alternatives.”
Young explains the growth to the west. “We can’t go to the east because that is Manitoba. We can’t go to the north because that is Mosaic, and as you go to the south the ore body dips and as you go south it gets too deep to mine you would have to look at solution mines for mining a deeper ore body because you get so much pressure on the ground from all the overhead burdens so the deeper the ore body gets, the more pressure on the ground, so at some point there is a line that it doesn’t make sense to mine.”
What makes the difference in Rocanville to make it the world’s largest potash mine?
“The quality of our ore body,” says Young. “We have very stable ground which allows us to do three pass mining. The ore grade is strong, but it really comes down to the ore body. Three pass mining is very efficient to do versus stress-relief chevron mining which is what some of our other sites do, so just the efficiency and the operating costs are very low. There are less hazards because there are no clay seams. When you run into those you’re doing a lot of bolting which is another added cost.”
Young says the Nutrien mine has operated outside of Rocanville for many decades.
“It has been here for 54 years and based on our public disclosures we will continue to be here for the long term. We do have more land to the northwest as well, so we’ll see.”